Technology Overview
PLASCON® does not use incineration, instead utilising pyrolysis in an inert environment, which is achieved through a patented plasma arc process.
Contaminants are eliminated with a destruction efficiency often surpassing 99.9999%, which exceeds the most stringent standards set by government agencies around the world.
No toxic off gases are produced. Emissions consist only of salty water, which in most cases can be released directly to the environment, and small quantities of carbon dioxide and carbon monoxide. This means that there is no need for costly post treatment scrubbing processes.
Process inputs are: electrical energy with a source requirement of 200kW, caustic soda, pure argon gas, which is used to sustain an inert reaction environment, and water for the gas scrubber.
Some key characteristics of the PLASCON® Process are:
- Continuous plasma arc process
- Computer controlled to guarantee optimum operating efficiency and safety
- Can operate 24/7 with no need for personnel to be continuously on hand
- Can operate in-situ as part of an industrial process or to destroy stockpiled feedstock
- Modular and compact. The units are designed to fit inside a standard 20 foot shipping container
- Start up (from cold) takes no more than ten minutes
- A routine shut down for regular maintenance can be completed and the process back on line in less than an hour
- Energy efficient
Plasma is an ionised gas. The plasma state is created when sufficient energy is added to a gaseous medium to the point where an electric current can be sustained. The plasma state is commonly observed in electric-arc welding where air is the plasma medium.
In the case of PLASCON® energy is transferred to the process in the form of a super hot argon plasma.
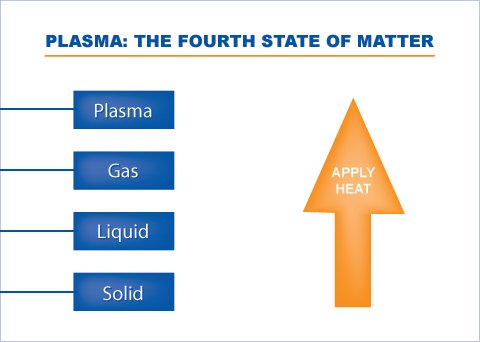
The heart of the PLASCON® process is a compact plasma torch developed by CSIRO and Siddons Ramset Limited and further refined by SRL Plasma Limited. The torch provides an extremely high energy density heat source into which liquid or gaseous waste is injected. The core of the plasma can reach temperatures in excess of 20,000°C. At these extreme temperatures the molecules of any waste material injected into the device break apart (dissociate) almost instantaneously. This process is known as pyrolysis. Unlike conventional combustion processes, a fuel is not required, nor is the addition of excess oxygen.
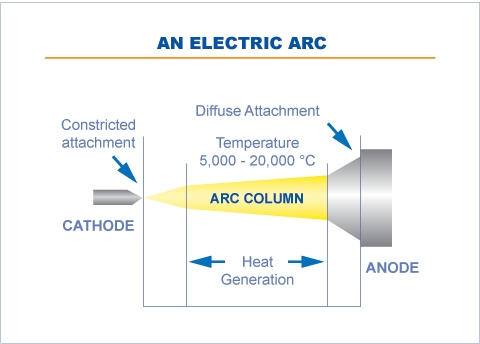
The products of pyrolysis pass down a reaction tube that provides sufficient residence time to ensure the complete decomposition of the feed material. The hot gases (approx. 1,200°C) exiting the reaction tube are rapidly cooled in a caustic quench thus converting the hot acid gases to harmless neutral salts. The short residence time at the high temperature in the reaction tube (peak temperature >3,000°C) followed by rapid quenching prevents the formation/re-formation of dioxins/furans and other undesirable organic compounds. Examples of the decomposition chemistry can be found in the case studies.
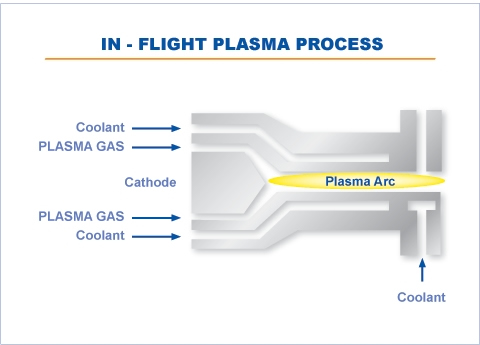
Atmospheric emissions from the process are typically argon, carbon dioxide and traces of carbon monoxide. Residual acid gases are neutralised in the gas scrubbing system.
In comparison with incineration processes, the off-gas volumes from PLASCON® are extremely low, as are residual ground level concentrations.
PLASCON® can achieve Destruction Efficiencies (DE) in excess of 99.9999%.
Destruction Efficiency definition: The overall destruction performance calculated on the basis of the total weight of waste input to the process, minus the sum of the waste in all products, by-products and environmental releases, divided by the waste input. (DE is reported as a percentage).